Health Care & Pharma
High-purity mineral salts for pharmaceuticals and valuable ingredients for personal care.
We provide the pharmaceutical and medical industries with a broad range of mineral salts (including Potassium, Magnesium, Sodium and Calcium). Our high-purity salts are used in fluid, semi-fluid and solid dosage forms.
The starting material for our high purity products are crude salts usually from mining and hence of natural origin. To obtain the highest purity levels, all salts are carefully refined in complex processes. In addition, they are continuously tested by us and third party laboratories for all relevant chemical and physical properties. In particular, this includes the requirements of the international pharmacopoeias.
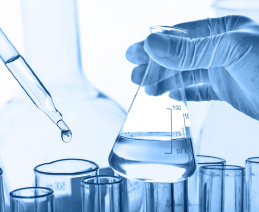
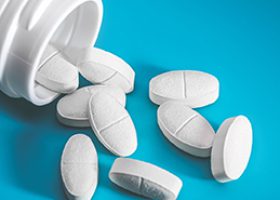
Epsom salt is widely used in spa treatments. Soaking in Epsom salt after hard exercise is often recommended by sports coaches and athletes. The magnesium and sulfate from the Epsom Salt are easily absorbed through the skin and the magnesium helps improve blood flow and relax your muscles and extremities.
For manufacturers of cosmetic and personal care products, we provide perfect mineral ingredients. Mineral salts perform numerous functions: they are used as skincare agents, humectants, keratolytic agents and buffers. They control a product’s viscosity, to preserve it or to act as deodorants and antiperspirants.
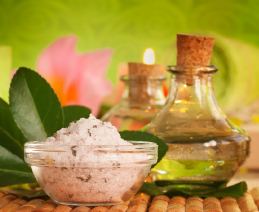
Active ingredients
Our top of the class Saltosil-K product line with or without anti caking agent. Highest purity for many different pharmaceutical applications, complies with the European and US-American pharmacopoeias (Ph. Eur. and USP).
- Saltosil-K, Potassium Chloride, 99.9%, Ph. Eur., USP, without anti-caking
- Saltosil-K, Potassium Chloride, 99.9%, Ph. Eur., USP, with anti-caking
Our top of the class Saltosil-KS product line. Highest purity for many different pharmaceutical applications, complies with the European and US-American pharmacopoeias (Ph. Eur. and USP).
- Saltosil-KS, Potassium Sulfate, 99.9%, Ph. Eur.
Our top of the class Saltosil-Na product line.The particularly high, very pure quality for API, complies with the European and US-American pharmacopoeias (Ph. Eur. and USP).
- Saltosil-Na, Sodium Chloride, 99,9%, Ph. Eur. USP
The microgranulated high purity Magnesium source for cosmetics and bathing (bath salt).
- Saltosil-MgS, Magnesium Sulphate Heptahydrate, Ph. Eur.
txt update coming soon
- Magnesium Peroxide Ph. Eur.
- Calcium Peroxide Ph. Eur.
Excipients & Colors
USP/Ph.Eur/JP/BP/IP
- Micro Crystalline Cellulose (MCC) 101
- Micro Crystalline Cellulose (MCC) 102
- Micro Crystalline Cellulose (MCC) 112
- Micro Crystalline Cellulose (MCC) 200
- Micro Crystalline Cellulose (MCC) 301
- Micro Crystalline Cellulose (MCC) 302
- silicified Micro Crystalline Cellulose (sMCC) 101
- silicified Micro Crystalline Cellulose (sMCC) 102
- Powder Cellulose (PC)
- Micro Crystalline Cellulose Gel (RC Type)
- OptiWhite natural CC
Medical Care
Our top of the class Saltosil-K product line with or without anti caking agent. Highest purity for many different pharmaceutical applications, complies with the European and US-American pharmacopoeias (Ph. Eur. and USP).
- Saltosil-K, Potassium Chloride, 99.9%, Ph. Eur., USP, without anti-caking
- Saltosil-K, Potassium Chloride, 99.9%, Ph. Eur., USP, with anti-caking
Our top of the class Saltosil-Na product line.The particularly high, very pure quality for API, complies with the European and US-American pharmacopoeias (Ph. Eur. and USP).
- Saltosil-Na, Sodium Chloride, 99,9%, Ph. Eur. USP
Health Care
The microgranulated high purity Magnesium source for cosmetics and bathing (bath salt).
- Saltosil-MgS, Magnesium Sulphate Heptahydrate, Ph. Eur.
Personal Care
- Micro Crystalline Cellulose (MCC) 101
- Micro Crystalline Cellulose (MCC) 101
- Powder Cellulose (PC)
- Micro Crystalline Cellulose Gel (RC Type)
- OptiWhite natural CC
Our top of the class Saltosil-Na product line.The particularly high, very pure quality for API, complies with the European and US-American pharmacopoeias (Ph. Eur. and USP).
- Saltosil-Na, Sodium Chloride, 99,9%, Ph. Eur. USP:
The microgranulated high purity Magnesium source for cosmetics and bathing (bath salt).
- Saltosil-MgS, Magnesium Sulphate Heptahydrate, Ph. Eur.
Additional Information on our MCC Types
Our MCC qualities are spray dried only to provide you the best performance at your production process. Our MCC offers a superior flow characteristics, porosity, uniform particle sizes distribution, better compressibility, faster disintegration and low friability.
In addition to that we keep the lowest dark particle controls which can even be specified on the COA.
Risk Management:
We help to de-risk the use of excipients, in line with QbD (ICH Q8/9) by:
- Creating batch-to-batch consistent and reproducible products taking into consideration FRC’s (EP) and/or CMA’s (USP)
- Complying to 3 sigma technology to ensure consistency in meeting said FRC’s (EP) and(or CMA’s (USP) like bulk density, particle size distribution, moisture content, etc.
Available Regulatory Information:
- EXCiPACT, DIN ISO 9001, GMP
- US DMF, CN DMF
- Complying to JP/USP/Ph.Eur./BP
High Innovative Technology: Our sMCC Product Line
Our sMCC is a co-processed excipient compromising eccentric combination of MCC and colloidal Silicon dioxide. It delivers functional synergies and avert many common problems durning high speed tabletting and direct compression while using sticky or oily APIs. We consider sMCC as the next major step for the modern formulation process. Further more it helps every top of the class manufacturer to launch products quicker to the market, to form smaller tabletts and to improve the cost basis at R&D. Overall a win-win excipient for the pharmaceutical industry.
Summery:
Overall our top of the class MCC and sMCC product line will help you to save costs in the full range of your production process, while minimizing risk, providing you a quicker launch to the market of your products.
USE CASE I: Spray Dried MCC Vs Bulk Dried MCC in the Tabletting Process
IN PROCESS PARAMETER
- Flowability
- Porosity
- Control on PSD
- Segregation tendency
- Cohesivity
SPRAY DRIED MCC
Higher
Higher
Superior
Lesser
Lesser
BULK DRIED MCC
Less
Less
Inferior
Higher
Higher
TABLETTING PROPERTIES
- Compressibility/Hardness
- Compaction forces
- Disintegration Time
- Weight Variation
- Suitable for High Speed Tabletten
- Dwell Time Impact
- Production Output
- Machine Wear and Tear
SPRAY DRIED MCC
Higher
Lower
Faster
Low
More Suitable
Less Impact
Higher
Less due to lower compaction forces
BULK DRIED MCC
Lower
Higher
Slower
High
Less Suitable
More Impact
Lesser
Higher on the long run
Economics
- Overall Costs
- R&D Savings
- Purchasing Costs
- Maintenance Costs
- Addition Cost for WG instead of DC
SPRAY DRIED MCC
Lower
Significant
Higher
Low
Less properly
BULK DRIED MCC
Higher
Low
Lower
High
Properly
USE CASE II: SILICIFIED MCC Vs MCC in the Tabletting Process
IN PROCESS PARAMETER
- Flowability
- Porosity
- Control on PSD
- Segregation tendency
- Cohesivity
sMCC
Higher
Higher
Superior
Lesser
Lesser
MCC
Less
Less
Inferior
Higher
Higher
TABLETTING PROPERTIES
- Compressibility/Hardness
- Compaction forces
- Disintegration Time
- Weight Variation
- Suitable for High Speed Tabletten
- Dwell Time Impact
- Production Output
- Machine Wear and Tear
sMCC
Significant Higher
Significant Lower
Faster
Low
Perfect
Less Impact
Higher
Less due to lower compaction forces
MCC
Lower
Higher
Slower
High
Suitable
More Impact
Lesser
Higher on the long run
Economics
- Overall Costs
- R&D Savings
- Purchasing Costs
- Maintenance Costs
- Addition Cost for WG instead of DC
- Fewer other Excipients
- Easier Formulation Development
- Less Scale Up Time
- Quicker Product launch to the Market
sMCC
Lower
Significant
Higher
Low
Not Properly
Yes
Yes
Yes
Yes
MCC
Higher
Low
Lower
High
Properly
–
–
–
–
Extended Product Advantages
- Suitable for oily and sticky APIs
- Suitable for natural/herbal extracts
- Suitable to manufacture smaller tabletts
sMCC
Yes
Yes
Yes
MCC
In some cases
In some cases
–
Available Products by Application (TABLETTING)
Application
WET GRANULATION
DIRECT COMPRESION
HIGH DENSITY
LOW MOISTURE
Product Grades
PH 101
PH 102
PH 200
SMCC 50
SMCC 90
PH 301
PH 302
SMCC 90 HD
PH 102 LM
PH 103
PH 112
PH 200 LM
PSD (microns)
50
100
170
50
125
50
100
125
100
50
100
170
LOD (%)
NMT 6.0
NMT 6.0
NMT 6.0
NMT 6.0
NMT 6.0
NMT 6.0
NMT 6.0
NMT 6.0
NMT 3.0
NMT 3.0
NMT 2.0
NMT 3.0
Bulk Density (g/ml)
0.26 – 0.33
0.26 – 0.33
0.28 – 0.36
0.25 – 0.37
0.25 – 0.37
0.34 – 0.45
0.35 – 0.46
0.38 – 0.50
0.26 – 0.33
0.26 – 0.33
0.26 – 0.33
0.28 – 0.36
Available Products by Application (Capsule Filling)
Application
STANDARD & HIGH SPEED FILLING
Product Grades
PH 102
PH 200
PSD (microns)
100
170
LOD (%)
NMT 6.0
NMT 6.0
Bulk Density (g/ml)
0.26 – 0.33
0.28 – 0.36